文章来源:整理自中信证券研报、财通证券研报、华福证券研报、华创证券研报、中商情报网、行行查、CIOE2024展会资料、网络资料
CIOE中国光博会今年特别联动SEMI-e深圳国际半导体展,聚焦半导体上下游产业链,集中展示半导体材料、多种类半导体设备、半导体设备核心部件、光学系统、第三代化合物半导体材料及加工设备、IC设计/芯片及应用、分立器件、光电子器件、传感器等,展会同期将举办光电子集成芯片、纳米压印、超精微纳、半导体光学检测、真空镀膜、激光赋能半导体智造等多场半导体相关主题论坛。光电产业作为现代科技的核心领域之一,不断涌现出创新成果与应用前景广阔的技术亮点。将于9月10-12日在深圳国际会展中心举办的CIOE中国光博会紧抓技术热点,特别开设“光电热点技术”专栏,深度聚焦光电产业与热点技术互相融合,探索其在各领域的创新应用,共同展望未来发展趋势。
本期为第二期:半导体光学,在光与半导体的精密耦合中,一轮科技革新蓄势待发...
半导体加工制造拥有十大类设备,其中光刻机和量/检测设备为半导体制造的重要设备。设备升级推动技术节点进步,伴随着集成电路产业的发展,半导体光学产业应运而生,逐渐形成了单独的半导体光学产业链。在半导体制造过程中,生产一个合格器件需要数百道处理步骤,每道工序均需要使用相关设备进行制造以及良率控制。根据KLA(科天半导体),半导体量/检测基本覆盖半导体制造全流程, 其中量/检测设备原理以光学检测为主,每道步骤都必须完美执行,以避免产生致命缺陷产生。此外,对于半导体器件而言,光刻为结构形成的重要环节,光刻系统作为光刻机关键组成直接影响制程、速度以及良率。因此,精密光学系统对于制造工艺以及良率控制有重大影响,为半导体设备的核心系统。作为光刻机与量检测设备重要组成,精密光学系统决定集成电路工艺制程节点,覆盖半导体制造全流程。
光刻机光学子系统是半导体光学系统的核心,包括光源、照明系统和物镜系统。光刻机工作时,光源发出的光束经照明系统后穿过掩模版,再由投影物镜系统将掩模版上的电路图形复制到硅片表面。
光源是光刻机的核心构成之一,其波长决定了光刻机的工艺能力。光刻机根据光源不同可分成紫外(UV)光刻机、深紫外(DUV)光刻机、极紫外(EUV)光刻机三类,光源波长越短对应制程节点越先进,技术难度也越高。
• 紫外光刻机 :采用汞灯,从g-line到l-line,波长从436nm至365nm,制程节点为800-250nm。高压汞灯是气体放电电光源,采用汞蒸气发电放光。由椭球面反射镜、高压汞灯、快门、准直透镜、滤光镜、复眼透镜等组成。资料来源:《紫外LED光刻光源系统的研究与设计》——王国贵,华福证券研究所• 深紫外光刻机:采用准分子激光,从KrF到ArF/ArFi,对应波长为 248nm-134nm,制程节点为180nm-7nm。准分子激光器光源较汞灯光源的波长更短、光子能量更大、平均功率更高、稳定性更强,可满足更高的IC集成需求。资料来源:《紫外LED光刻光源系统的研究与设计》——王国贵,华福证券研究所• 极紫外光刻机:是下一代光刻技术的一种,在7nm 以下的最高端工艺上都会采用EUV 光刻机。由高能激光轰击金属锡产生等离子体辐射产生。工作原理:将二氧化碳激光照在一束快速射出的熔融态锡滴上,利用脉冲激光辐照锡靶,使其蒸发电离并产生高密度的等离子体,从而辐射出极紫外光。资料来源:Carl Zeiss SMT GmbH workshop,中信证券整理位于光源和物镜系统之间,其作用是将光源发出的光束进行整形匀化后,为掩膜提供成像曝光所需的照明模式和照明光场,再由投影物镜系统将掩模面上的图形复制到硅片表面。其组件包括光瞳整形透镜、匀光单位、扫描狭缝和中继镜。光源经过扩束准直与传输后进入光瞳整形单元,然后再经过照明匀化单元来实现特定分布的照明光场,随后,扫描狭缝用来确定曝光视场尺寸和中心位置,控制曝光剂量,并与掩模台和硅片台完成同步扫描曝光。中继镜组位于扫描狭缝与掩模板之间,负责将扫描狭缝上的照明光场中继成像到掩模面上。
资料来源:《光刻机照明系统中继镜组的光场均匀性优化设计》——龚爽,华福证券研究所整理空间光阑滤波是一种简单低成本的光瞳调制方式,在照明光瞳处设置一组光阑挡片来改变光瞳形状,一般包括不同通光孔径的传统和环形模式。
微透镜是通过一组紧密排布的复眼阵列,对光束进行微切割后重组,从而实现匀光。匀光棒是利用了光在介质里的全反射原理实现匀光。
扫描狭缝用来确定曝光视场尺寸和中心位置,系统利用狭缝阻挡光线,减少光的散射,并且可以改进曝光的分辨率,控制曝光剂量。狭缝单元设置在一次照明面,通过 XY 两个方向的刀口运动实现对照明视场的控制。
中继镜组是对一次照明面的光束进行中继放大,负责将扫描狭缝上的照明光场成像到掩模面上。中继镜不仅需要满足不同光瞳大小和环宽的照明模式需求,并且要尽量减少照明光场不均匀性在中继过程中的恶化。资料来源:《照明光瞳调制技术研究》——高爱梅,华福证券研究所整理物镜系统的功能是实现光线的聚焦以将掩膜版上的图形缩放至晶圆表面。投影物镜是光刻机中最昂贵、最复杂的核心部件之一,为了精确成像,严格控制像差,光刻机透镜平整度和光洁度要求度极高。高数值孔径的镜头决定了光刻机的分辨率以及套值误差能力。物镜系统的主要作用是把掩膜版上的电路图按比例缩小,再被激光映射到硅片上,并且物镜还要补偿各种光学误差。物镜由 20 多块镜片组成,分为全反射型、全折射型、折反射型多种结构型式:在目前的高分辨率光刻机中,以全折射式结构型式为主流。与全折射式结构型式相比,折反射式结构的投影物镜具有许多优越的学性能,但其在光刻机中的真正使用尚需克服许多技术问题。采用全球面结构,步进物镜孔径尺寸随NA急剧增加,同时设计复杂程度增加,因此,随物镜NA的继续增加,尤其当NA大于0.7时,物镜的设计引入非球面。非球面的使用能够在不增加独立像差数的前提下,增加自变量个数,有利于改善像质。在同等约束条件下,减少了光学元件的数量,降低了光学系统尺寸和重量。对于NA>1.2的投影物镜,大多采用折反式光学系统。折反式系统在物镜结构设计中加入凹面反射元件。凹面镜的使用能够很好的满足场曲的矫正,而不需要大光焦度的负透镜和孔径较大的正透镜来满足场曲的矫正,进一步降低了物镜的体积。资料来源:《193nm投影光刻物镜光机系统关键技术研究进展》——张德福等、华福证券研究所整理前道制程和先进封装的质量控制可划分为检测(Inspection)和量测(Metrology)环节。检测指在晶圆表面上或电路结构中,检测其是否出现异质情况,如颗粒污染、表面划伤、开短路等对芯片工艺性能具有不良影响的特征性结构缺陷;量测指对被观测的晶圆电路上的结构尺寸和材料特性做出的量化描述,如薄膜厚度、关键尺寸刻蚀深度、表面形貌等物理性参数的量测。根据检测类型的不同,半导体质量控制设备分为检测设备和量测设备。检测+量测环节贯穿前道制程和先进封装全过程,光刻和刻蚀等工艺均需至少7种类型量/检测设备。量/检测设备主要应用于前道制程和先进封装,基本覆盖了各子环节,是保证芯片生产良率的关键要素之一。半导体量/检测包括光学检测、电子束检测和X光量测等技术。半导体光学量/检测设备适用场景丰富,在半导体先进制程当中应用广泛。在检测环节,光学检测技术可进一步分为无图形晶圆激光扫描检测技术、图形晶圆成像检测技术和光刻掩膜板成像检测技术。在量测环节,光学检测技术基于光的波动性和相干性实现测量远小于波长的光学尺度,集成电路制造和先进封装环节中的量测主要包括三维形貌量测、薄膜膜厚量测、套刻精度量测、关键尺寸量测等。与光刻机工作时直接成像的光学原理的不同,光学量检测设备广泛采用非直接成像原理。量检测设备由多个入射通道(波长、入射角、照明方式等不同)和多个信号收集通道(散射光、衍射光、反射光等、宽窄等),组合成不同的工作模式。通过监测不同模式下的光谱信息,再使用算法对晶圆表面逆向成像,从而发现晶圆表面的缺陷或测量参数。非直接成像方法,较少受制于光波长带来的衍射极限;但对检测波段、光束偏振态、照明光束截面形状、物镜NA 值、探测器灵敏度等有极高的要求。先进制程的量检测过程中,待测参数增多带来额外挑战。光刻机内置的套刻误差测量组件也在不断提高精度中遇到了类似的问题。半导体光学产业的发展和上述挑战,对光源,相机/传感器,运动平台,算法等光学组件提出了更高的要求。资料来源:《Structural Design and Simulation of a Multi-Channel and Dual Working Condition Wafer Defect Inspection Prototype》(Ruizhe Ding 等),财通证券研究所资料来源:Jadak Tech,《SPIE》(Erin M. Schadt)财通证券研究所量检测设备与光刻机使用的光源性能存在较大区别,主要原因为:光刻过程中激光直接照射掩膜版与光刻胶,量检测过程中,光罩检测会照射掩膜版,其他量测的激光的照射对象通常为硅、硅化物、金属等,其光学属性存在较大区别;其次工作目的不同,光刻曝光过程直接改变光刻胶的理化性质;量检测需尽可能避免对集成电路结构的改变或损伤,故其激光能量一般低于光刻用准分子激光,通常采用全固态激光。全固态激光具有线宽窄、体积小、稳定性高、光束质量好等优点。晶圆表面缺陷尺寸小、缺陷物质种类多,高检出率需要检测光源须同时具备高亮度、宽光谱范围等特点。为满足上述需求,激光维持等离子体(LSP)光源应运而生,广泛应用于明场缺陷检测设备中。LSP 光源利用导入的外部激光和曲面聚焦收集镜,形成外部激光辐射场。高压Xe 灯中激光与电离气体相互作用产生的等离子体,从聚焦在等离子体区域的外部激光辐射场中吸收能量,维持在接近热力学平衡状态;等离子在内部的电子跃迁过程中发出等离子激光。LSP 光源体积小、能量沉积效率高,同等功率下光源发光强度高,且寿命更长。
晶圆缺陷检测过程中,所需光学信号获取,多数由时域延迟积分(TDI)相机完成。TDI相机以“线”为单位进行图像采集。TDI相机的原型单线扫描相机只有一行感光像素,随着检测速度的提高,相机的曝光时间被不断缩短,多线感光的TDI线扫描相机逐渐成为主流。TDI相机属于工业相机的分支,当前TDI线扫描相机图像传感器输出分辨率已经达到了24K,面扫描相机分辨率达2亿像素以上,数据位宽也从最初的8bi逐步发展到10bit乃至16bit。搭载了FPGA 和DRAM 芯片的工业相机,其前端嵌入式运算能力进一步加强,更多的复杂计算可以在相机端实现。借助像素位移技术和超分辨率算法,相机可实现4倍或更高分辨率的图像合成。
但TDI相机的应用,也存在一些局限。其成像原理对镜头和光源要求较高,加大了系统开发的难度和成本;TDI 相机需要运动控制与反馈系统支持,扫描过程中被检测物体需接近匀速运动,否则图像精度可能降低,最终影响量检测的精度。TDI相机对运动精度和速度的要求,需要通过先进的运动平台系统实现。光刻与量检测过程中的精确定位和位移,由高精密运动平台(光刻机中称双工件台)系统实现。运动平台系统具备工装夹取、移载、定位等功能,也可用于晶圆键合、晶圆切割等工艺。
以光刻工件台例,运动平台采用了多项特殊设计,以满足半导体光学的工艺要求。高度轻量化:为降低运动惯量,减轻电机负载,提高运动效率,运动平台普遍采用轻量化结构设计,轻量化最高可达到90%;高形位精度:为实现高精度运动和定位,运动台结构具有极高的形位精度;高尺寸稳定性:运动台结构件不易因为温度或力度而变形;清洁无污染:运动台具有极低的摩擦系数,动能损失小,无磨削颗粒的污染。上述特殊设计,需要激光干涉/平面光栅测量,特种光学元件加工,先进材料,多层压电驱动器等多项关键技术支持。激光干涉仪以激光波长为基准,具有高精度和可溯源性。测量运动平台多自由度位移,需采用多台激光干涉仪,搭建多自由度测量系统。激光干涉仪定位存在光路较长的缺点,受环境影响会导致的纳米级的误差,正被光栅干涉法部分替代。光栅干涉仪以光栅的栅距为基准,利用光栅的衍射效应实现对工件台的单点多自由度测量。由于光栅仪的光路较短,环境适应性强,可满足3-5nm 制程光刻机超精密定位的需求。光刻机工件台的方镜用于承载晶圆,同时也是多轴激光干涉仪的目标反射镜,对于精确定位至关重要。方镜对反射面的面形精度、位置精度、整体刚度等都具有极高的要求,对其参数测量需要20 余种通用及专用测量仪器。原材料方面,工件台本体常采用铝合金或碳化硅(采用碳化硅的性能优于铝合金);殷钢作为测量系统的基座;机械和热学性能出色的肖特微晶玻璃用于制造方镜。微晶玻璃在EUV 光刻中容易破损导致精度下降;其在维持刚度时需增加厚度,无法实现轻量化;堇青石或碳化硅陶瓷未来有望成为替代材料。
多层压电驱动是另一项关键技术:对压电陶瓷施加电压,其会产生位移形变,具有纳米级位移分辨率,且响应快、体积小、扭力大、无电磁干扰的优势。多层压电驱动应用在镜片微调、掩模台或运动台位置调整、主动减振等环节。
展会现场不仅将展出各类精密光学元件,同时还有超全的半导体光学元件的精密光学加工设备亮相。
精密光学制造居于半导体光学产业链位的核心地位,支撑几乎所有半导体光学元件的生产。除用于半导体领域外,工业级精密光学制造主要服务于航空航天、生命科学及医疗、无人驾驶、生物识别、AR/VR 检测设备等产业。半导体领域,极紫外光刻正成为集成电路制造的核心技术,对光学元件面型精度的要求达到λ/200,表面粗糙度低于0.1nm,这些指标达到或超过了当前精密光学加工技术的极限,属于超精密级别。德国、日本、美国占据超精密光学制造技术制高点,德国蔡司是半导体全球光学代表性企业。超精密光学制造由超精密光学加工、超精密光学镀膜、超精密光学检测、超精密装调等环节构成。
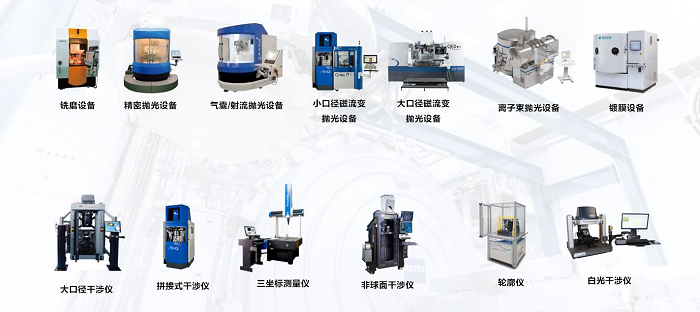
资料来源:中科院光电技术研究所,国科精密,NTG 官网,布勒莱宝光学官网,斯图加特大学官网,财通证券研究所

资料来源:各公司官网,CIOE 官网,财通证券研究所
IC载板(Integrated Circuit Substrate)是半导体封装中不可或缺的关键基材,主要用于支撑和连接集成电路芯片与外部电路之间的电气互联,不仅承担着电气信号的传输和机械支撑的作用,还对芯片的散热、抗干扰能力以及封装的尺寸和稳定性等方面具有重要影响。
玻璃基板(Glass Substrate )是一种以高透明度、优异平整度及良好稳定性为特点的基底材料,其主要功能是作为支撑载体,确保上层功能材料的可靠固定和良好的电气、光学性能,从而保障整个器件或系统的长期稳定性和使用寿命,被视为半导体、显示领域新一代基板解决方案。英特尔、三星、AMD、日本DNP、沃格光电、厦门云天半导体等国内外玩家竞相涌入玻璃基板赛道。
TGV(Through Glass Via )玻璃通孔技术是一种用于玻璃基板的垂直电气互连技术,是玻璃基板封装的核心技术。TGV的出现,旨在解决传统TSV转接板中由于硅衬底的高损耗问题所引发的高频或高速信号传输性能下降,以及硅材料成本较高、工艺复杂等挑战。近年来,随着技术的不断发展,TGV的性能已逐步提升,并已在多个领域得到应用。主要的应用领域包括传感器、中央处理器(CPU)、图形处理器(GPU )、人工智能(AI)芯片、显示面板、医疗器械及半导体先进封装等。
TGV技术工艺流程图
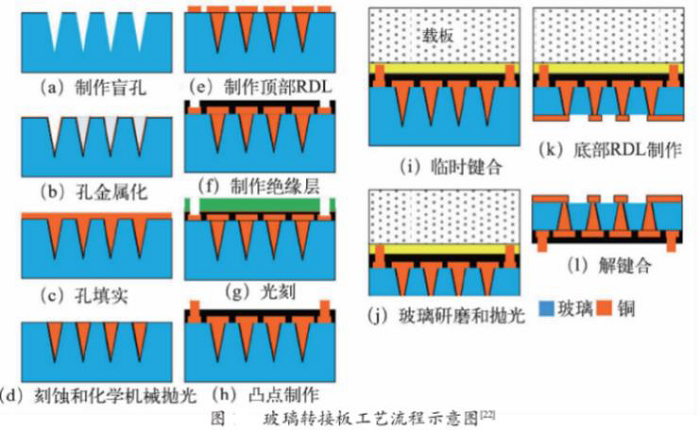
资料来源:陈力等《玻璃通孔技术研究进展》、华创证券
TGV结合多种工艺流程实现3D互联。TGV工艺包括种子层溅射、电镀填充、化学机械平坦化(CMP)、重新分布层(RDL)布线以及凸点(bump)工艺引出等。TGV通常采用直径在10μm至100μm之间的微型通孔。对于先进封装应用,每片晶圆上通常需要数万个TGV通孔,并对其进行金属化处理,以确保所需的导电性能。与传统的TSV工艺相比,TGV具有多项优势,主要包括:出色的高频电学特性、可获取的大尺寸超薄玻璃衬底、优异的机械稳定性等。特别是在高频应用场景中,TGV表现出比硅更低的损耗,能够有效提高信号传输质量。然而,TGV技术也面临一些挑战。最主要的问题是玻璃材料缺乏类似于硅的深刻蚀工艺,这使得在玻璃基板上快速制作高深宽比的通孔变得较为困难,这在一定程度上限制了其在某些高密度封装应用中的广泛使用。
国内外布局 TGV 技术厂商情况
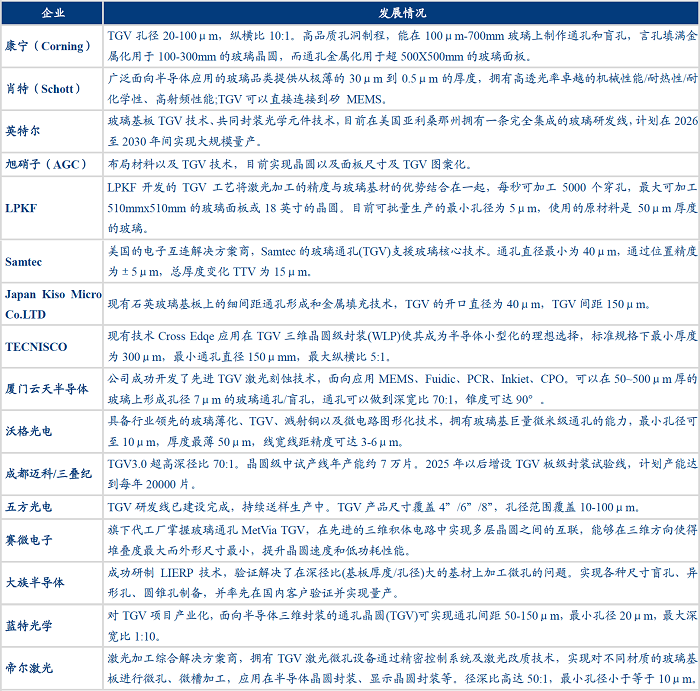
资料来源:半导体在线,势银芯链,公司公告,公司官网,华创证券
近年来,半导体制造领域的竞争日益激烈,数十年来,在DUV、EUV光刻机的支持下,摩尔定律得到了延续。迭代至今,面对芯片晶体管线宽已趋近物理极限,以及EUV光刻机产能有限、成本高等问题,业界开始加强探索绕开EUV光刻机生产高端芯片的技术和工艺,在此背景下,纳米压印技术逐渐走进人们的视野。纳米压印技术凭借其高分辨率、高产量以及低成本的显著优势,被国际器件与系统路线图(IRDS)组织选为下一代光刻技术的候选方案。纳米压印技术(Nanoimprint Lithography, NIL)是一种新型的微纳加工技术。它的工作原理与传统的光刻技术完全不同。传统的光刻技术用辐射(光或电子)曝光光刻胶和用化学冲洗来形成图案。而纳米压印用机械变形-压印来形成图案。纳米压印将预先图形化的模具压进与涂布好的纳米压印胶, 从而在纳米压印胶上复制出模具上的结构图案。为了减少压印的压力,纳米压印胶需要在压印时非常软 -如水一样(液态聚合物)。纳米压印胶有加热型:胶在加热时变软但冷下来变硬;有紫外光照型:胶在光照前时是软但光照后变硬;及热光混合型。压印后,模具和纳米压印胶分离-脱模过程。
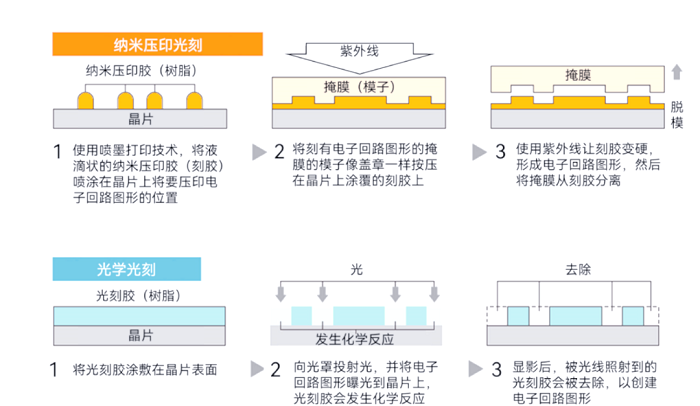
与传统光刻技术相比,纳米压印技术有其许多制造优势是传统的光刻技术无法相比的。比如,超高的高分辨率 (0.3 nm ), 高密度 (<6 nm 半间距), 3D 图案成型结构,无光学散射, 大面积, 兼容柔性衬底, 设备工艺简单,低能耗, 及高效、低成本的优势。这使纳米压印逐步成为大规模生产纳米结构的关键技术之一,现在已被广泛应用于LED、AR/VR、光学器件、生物医学检测等多个领域。去年9月,佳能公司已向美国德克萨斯州德克萨斯电子研究所(TIE)运送了其最新研发的纳米压印光刻(NIL)系统。纳米压印技术以其独特的创新性和前瞻性,为半导体产业带来了全新的光刻方案,不仅带来了新的发展机遇,也催生了行业内的挑战与变革。当然,纳米压印技术仍需在诸多方面进行完善与优化。尽管如此,其巨大的潜力和价值不容忽视。该技术有望降低半导体制造的门槛,让更多企业和国家能够涉足这一领域,从而打破ASML的垄断地位,推动半导体产业的多元化和激烈竞争,进而加速半导体技术的进步与创新。将于9月10-12日在深圳国际会展中心隆重举办的第26届中国国际光电博览会(CIOE 2025)今年特别联动SEMI-e深圳国际半导体展暨2025集成电路产业创新展,聚焦半导体上下游产业链,集中展示半导体材料、多种类半导体设备、半导体设备核心部件、光学系统、第三代化合物半导体材料及加工设备、IC设计/芯片及应用、分立器件、光电子器件、传感器等,即刻领取参观证件,一证参观光电及半导体产业双重盛宴!同时,CIOE展会现场还将举办多场半导体相关主题论坛,如:
高性能光电子集成芯片前沿技术论坛
ePIXfab中欧硅基光电子论坛